Деревянные оконные и балконные блоки
Оконные и балконные блоки из дерева
Оконный блок состоит из оконной коробки и оконных переплетов, которые включают створки, фрамугу и форточку. Оконную створку изготовляют из двух вертикальных и двух или трех горизонтальных брусков, связанных между собой в раму с помощью шиповых соединений, клея и нагелей. В створках, имеющих большие размеры, применяют горизонтальные бруски -- горбыльки, соединяющие вертикальные бруски. Горбылек имеет тот же профиль, что и брусок створки, но меньшую толщину. Он увеличивает прочность створки, однако уменьшает ее световую площадь.
В верхней части оконной коробки над створками, а иногда и в нижней части устанавливают горизонтальную рамку-фрамугу. Фрамуги бывают глухие и открываемые. При глухих фрамугах верхние притворы створок примыкают к четверти в нижнем бруске фрамуги. При открываемой фрамуге для ее крепления в оконную коробку вставляют горизонтальный брусок, называемый горизонтальным импостом.
В широких коробках делают вертикальный неподвижный брусок- вертикальный импост, к которому примыкают вертикальные кромки створок.
Форточку устраивают в верху переплета, но не выше 1,8 м от пола иначе ее будет трудно открывать. Устраивать форточку внизу переплета нежелательно- это вызывает сквозняки.
В зависимости от числа створок оконные переплеты различают одно-, двух- и трехстворчатые.
В двухстворчатых переплетах обе створки навешивают на петли, а в трехстворчатых на петли навешивают все три створки или две крайние, тогда средняя створка делается глухой, то есть не навешивается на петли.
Оконные створки могут открываться внутрь помещения или в разные стороны. Оконные створки, открывающиеся внутрь помещения, более удобны в эксплуатации, так как их легко мыть, остеклять, открывать и закрывать. Оконные створки, открывающиеся в разные стороны, в настоящее время почти не применяются.
Переплеты в окнах бывают внутренние и наружные. Для того чтобы створки хорошо раскрывались, размеры по высоте и ширине внутренних переплетов по сравнению с наружными делают на 50-75 мм больше. Разницу между размерами внутреннего и наружного переплетов называют рассветом.
Переплеты бывают с наплавом, то есть с напуском на брусок коробки, создающим более плотный притвор и закрывающим щели, которые образуются между створкой и коробкой. Наплав делают во внутренних или в обоих переплетах, что придает окнам более красивый вид.
Для переплетов с наплавом размеры внутреннего переплета делают больше наружного по высоте не 75 мм, а по ширине-на 75-100 мм.
Оконные и балконные блоки бывают различных конструкций, но наиболее широко применяют оконные и балконные блоки с двойными раздельными и со спаренными переплетами и полотнами.
Оконные блоки с двойными раздельными переплетами состоят из коробки, в которой навешены переплеты, открывающиеся в одну или в разные стороны. Для переплетов, открывающихся в одну сторону, расстояние между стеклами наружных и внутренних переплетов должно быть для жилых зданий 122, а для общественных- 140 мм.
Оконные блоки со спаренными переплетами состоят из двух переплетов - наружного и внутреннего, навешенных
вплотную между собой на петли, а внутренний, кроме того, - на петли к коробке. Соединенные между собой стяжками переплеты составляют как бы один переплет, имеющий достаточную жесткость.
Для мытья стекол внутренний и наружный переплеты раскрывают, развинчивая стяжки.
Отсутствие в спаренных переплетах горбыльков, горизонтальных импостов и фрамуг увеличивает их световую площадь, что повышает освещенность помещения и придает зданию архитектурную выразительность. Расстояние между стеклами спаренных переплетов 53 мм.
Оконные блоки с открываемыми (распашными) створками имеют ряд недостатков: узкие створки уменьшают световую площадь переплетов, а широкие при открывании загораживают внутри значительную часть помещения. В отдельных зданиях применяют деревянные окна со спаренными створками, вращающимися на средних горизонтальных осях (окна среднеподвесные) или на средних вертикальных осях (окна среднеповоротные).
Оконные блоки изготовляют с неравными и равными створками. В оконных блоках с неравными створками узкая створка заменяет форточку, оконные блоки с равными створками бывают с форточками и без них. Окна со спаренными переплетами (серии С) делают с наплавом, а с двойными раздельными переплетами и полотнами (Серии Р) - с наплавом или без него.
Оконные и балконные дверные блоки маркируют на предприятии-изготовителе. Марка состоит из буквенных индексов и цифр, обозначающих высоту и ширину проема в дециметрах. Буквенные индексы обозначают следующее: ОС - оконный блок со спаренными переплетами; ОР - оконный блоке двойными раздельными переплетами; БС - балконный дверной блок со спаренными полотнами; БР - балконный дверной блок с раздельными полотнами.
Оконные блоки с равными створками без форточек для жилых зданий и трехстворчатые для общественных зданий без фрамуг обозначают в конце марки буквой А.
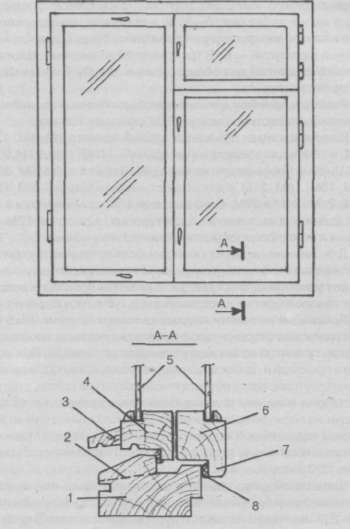
Рис. 1: Оконный блок со спаренными переплетами: 1 - брусок коробки (нижний); 2 - водоотводящая прорезь; 3 - отлив; 4 - брусок внешней створки; 5 - стекло; 6 - брусок внутренней створки; 7 - наплав; 8 - уплотняющая прокладка
Для оконных и дверных блоков, имеющих форточку или верхнюю фрамугу, в конце марки добавляют букву В; для блоков, имеющих верхнюю или нижнюю фрамугу - добавляют букву Г; для блоков с нижней фрамугой - Е. В трехстворчатых оконных блоках с верхней фрамугой для общественных зданий в конце марки добавляют букву И.
Размеры проемов для жилых и общественных зданий в основном соответствуют модулю 1М, равному 100 мм.
Высота проемов для жилых зданий принята 6М, 9М, 12М, 15М,и 18М, а для общественных зданий -12М, 18М,21М,27М.
Ширина проемов для жилых зданий принята 5М, 9М, 12М, 14М, 15М, 18М, 21М, а для общественных зданий - 9М, 12М, 18М, 21М, 24М и 27М. Окна высотой 15М применяются в жилых зданиях и частично в общественных, а высотой 12М - в кухнях и спальнях с повышенными подоконниками.
Для снижения воздухопроницаемости по периметру притвора в оконных переплетах и дверных балконных полотнах устанавливают уплотняющие прокладки. В качестве прокладок используют пенополиуретан, шерстяной шнур, губчатую резину и т. п.
Прокладки из пенополиуретана имеют сечение 10x8 мм. Одна широкая сторона такой прокладка покрыта слоем клея и закрыта лентой из антиадгезионного материала. При установке прокладки на место антиадгезионную ленту снимают, а прокладку прикладывают стороной, покрытой клеем, к наплаву створки окна или полотна балконных дверей. Когда прокладки из полиуретана не имеют клеевого слоя, то их ставят на клей повышенной водостойкости (КН-2, №88, «Момент», другие аналогичные полимерные клеи) при температуре не ниже 12°С в помещении.
Шерстяной шнур крепят к наплаву створки или полотна мелкими оцинкованными гвоздями длиной 12-16 мм с шагом 150-200 мм. Чтобы не смять шнур, гвозди забивают в край его по всему периметру створки или полотна, сохраняя постоянную толщину шнура. При закреплении шнур не стоит сильно натягивать, так как при этом он вытягивается, теряет упругие свойства и эластичность. Шерстяной шнур до установки пропитывают антимольным составом.
Прокладки из губчатой (пористой) резины крепят к наплаву створок, полотен на клее №88, «Момент» и т. п.
Прокладки должны быть упругими, прочными, светоморо-зостойкими и долговечными.
Для зданий, возводимых в первой и второй подзонах Северной строительно-климатической зоны, применяют окна и балконные двери с тройным остеклением и тройным уплотнением.
Окна для жилых зданий бывают одностворчатые и с узкими створками высотой 863, 1163, 1463 мм, а шириной 880, 1154, 1329, 1379, 1479, 2072 мм; с форточками-полуостровками высотой 1163 и 1463 мм, шириной 1154, 1329, 1379, 1479, 2072 и 2172 мм.
Оконный блок с тройным остеклением имеет три переплета, из которых один переплет одинарный - наружный, а друг гой спаренный - внутренний, створки имеют импостный и безимпостный притвор.
Створки спаренных переплетов высотой более 1400 или шириной более 800 (при высоте 1000 мм) навешивают на три петли - две верхние и одну нижнюю.
Остальные створки навешивают на две петли. Дверные полотна навешивают натри петли, располагаемые равномерно по высоте. Причем нижние и верхние петли крепятся на расстоянии 200 мм от верха и низа двери.
Для удобства пользования, снятия с петель створки-полуфорточки навешивают на врезные петли с вынимающимся стержнем.
Окна деревянные со спаренными створками, вращающимися на средних осях, подразделяются на два типа: вращающиеся на средних горизонтальных осях - среднеподвесные ОСГ, имеющие дополнительно вентиляционные клапаны или верхние фрамуги, и окна со створками, вращающиеся на средних вертикальных осях, - среднеповоротные ОСВ.
Подоконные деревянные доски устанавливают в жилых, общественных, производственных и вспомогательных зданиях. Подоконные доски имеют различный профиль обработки кромок. Они могут быть из цельной древесины или клееные. Размер доски по длине должен соответствовать ширине про-
ема с учетом заделки ее концов в стены не менее чем на 40 мм с каждой стороны.
Доски изготовляют из древесины хвойных пород. Применять древесину различных пород в одной подоконной доске, за исключением древесины сосны и ели, не допускается. Влажность древесины подоконных досок должна быть не более 9-15%. Заделки пороков древесины должны иметь влажность на 2-3% меньше нормируемой влажности досок, то есть от 6-7 до 12-13%.
При изготовлении клееных подоконных досок длина склеиваемых отрезков должна быть не менее 300 мм, а расстояние между стыками смежных склеиваемых элементов, располагаемых вразбежку по ширине подоконной доски, - не менее 150 мм.
Ширина делянок-досок, из которых склеивают подоконные доски, должна быть до 100 мм, причем во избежание коробления доски при склеивании чередуют по расположению годичных слоев.
Склеивать доски необходимо клеями повышенной водостойкости, а соединять склеиваемые отрезки по длине'- на зубчатый шип.
Лицевые поверхности досок окрашивают красками за два раза в белый цвет, а поверхности, примыкающие к стенам, ан-тисептируют.
Допускается вместо окраски облицовывать доски бумажно-слоистым декоративным пластиком светлого тона или строганым шпоном из древесины твердых пород, покрытых лаком.
Изготовление оконных блоков из дерева
Изготовление деревянных оконных блоков
Изучив чертежи, составляют спецификацию деталей с размерами в чистоте и заготовке. Затем по размерам, приведенным в чертежах, выпиливают заготовки для деталей окон и коробок ручными пилами, электропилами, на круглопильных или универсальных станках. После распиливания бруски стро-
гают рубанком, фуганком или фрезеруют электрорубанком, на фуговальных, рейсмусовых или комбинированных станках.
Затем проверяют прямоугольность и качество обработки брусков и приступают к их разметке.
Разметка. Размечают бруски с помощью метра, рейсмуса, малки, угольника. Шипы размечают с помощью шаблона.
Бруски размечают на разметочном столе с крышкой размером 2200x1600 мм (на 100-150 мм больше наибольшей длины бруска коробки).
Рассмотрим порядок разметки элементов оконного блока ОР15-15А с раздельными переплетами (рис. 1).
В оконном блоке ОР15-15А имеются наружная и внутренняя коробки. Для примера произведем разметку вертикального и горизонтального брусков внутренней коробки. В соответствии с чертежом вертикальный брусок должен иметь в чистоте длину 1464 мм, горизонтальный - 1495 мм.
Припуск на торцевание деталей с двух сторон при ширине до 150 и длине до 1500 мм дается 15 мм при получении деталей из заготовки и 35 мм - из пиломатериалов. Бруски, выпиленные из пиломатериалов, размечают так: два вертикальных или горизонтальных бруска кладут на стол лицевыми сторонами наружу, после чего от торца бруска отмеряют 18 мм, то есть припуск на оторцовку, а от него размер бруска подлине (в чистоте), что составит для вертикальных брусков 1464, а для горизонтальных - 1495 мм.
С помощью угольника наносят на брусок риски или карандашные линии. От последней карандашной линии наносят следующий припуск на оторцовку 17 мм (суммарный припуск на оба конца составляет 35 мм). Затем от линий оторцовки отмеряют размер, равный толщине шипов (в данном случае 44 мм), и также проводят риски.
Для выборки четверти размером 10-13x35 мм разметку делают следующим образом: от ребра бруска по пласти каждого бруска наносят риску, отстоящую на 35 мм, а по кромке - риску, отстоящую от ребра на 10 и 13 мл.
Вначале выбирают четверть размером 10x35 мм, а затем дополнительно снимают скос и доводят размер четверти до требуемого.
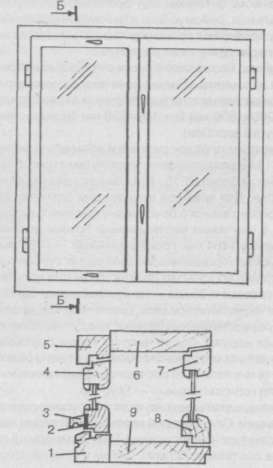 |
Рис. 1: Оконный блок ОР15-15А:
1 - нижний горизонт (брусок наружной коробки); 2 - нижний горизонт (брусок наружного переплета); 3 - отлив; 4 - верхний горизонт (фусок наружного переплета); 5 - профиль верхнего и боковых брусков наружной коробки; 6 - верхний горизонт (брусок внутренней коробки); 7 -- верхний горизонт (брусок внутреннего переплета); 8-нижний горизонт (брусок внутреннего переплета); 9 - нижний горизонт (брусок внутренней коробки)
|
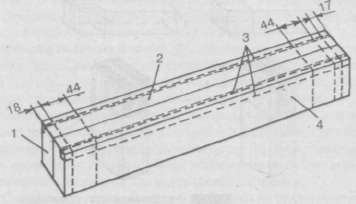 |
Рис. 2: Схема разметки вертикального бруска внутренней коробки ОР15-15А:
1 - брусок коробки; 2 - лицевая кромка коробки; 3 - линия разметки четверти; 4 - лицевая часть пласти бруска
|
Выбирать четверть можно ручным инструментом или на фрезерном станке. После выборки четверти бруски торцуют на нужный размер в чистоте.
Выпиловка шипов и проушин. При выпиловке шипов и проушин выполняют в строгой последовательности следующие операции: размечают шипы и проушины, запиливают их, выпиливают заплечики и выдалбливают проушины.
В соответствии с чертежом определяют размеры соединений, после чего приступают к разметке. Рассмотрим порядок разметки углового концевого соединения на открытый сквозной одинарный шип УК-1 для брусков толщиной 42 и шириной 65 мм.
Для соединения УК-1 толщина шипа должна быть равна 0,4 толщины бруска, а толщина проушины, соответственно, 0,5 от разницы толщины бруска и толщины шипа, то есть при толщине бруска 42 мм толщина шипа будет равна S1 = 0,4 х 42 = = 16,8 (округлим до четного числа 16 мм), а толщина проушины тогда будет S2 = 0,5 х (42 - 16) = 0,5 х 26 = 13 мм.
В соответствии с этим результатом размечают шипы.
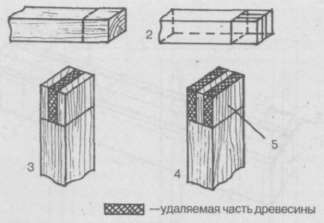 |
Рис. 3: Разметка шипов и проушин:
1 - разметка высоты шипов; 2 - разметка линий запили-
вания; 3 - проушина; 4 - шип; 5 - заплечико
|
Можно шипы и проушины размечать с помощью шаблонов, такой метод ускоряет процесс нанесения рисок на торцы брусков, а при массовых разметках предотвратит ошибки.
После разметки приступают к выработке шипов и проушин. Запил ивание ведут лучковой пилой, при этом необходимо тщательно проводить работу, иначе перекос шипа может привести к перекосу всей створки. Если шип толще проектного размера, то при посадке в проушину он может расколоть брусок, а если тоньше - соединение получится непрочным, так как шиповое соединение будет без плотной посадки.
При пилении следят за тем, чтобы полотно пилы проходило около намеченной риски, только в этом случае получится точный размер шипа или проушины. При выработке шипов нужно пилить только с наружной стороны рисок, а проушин - с внутренней.
При начале пиления для быстрого углубления полотно пилы ставят на ребро торцовой части бруска под углом 15-20° и, сделав несколько движений на себя, без нажима углубляют пилу, после чего пилят равномерно без рывков и особого нажима. Строго следят, чтобы полотно шло ровно вдоль риски. После произведенного пропила срезают заплечики.
Проушину после запилов выдалбливают долотом с киянкой.
Элементы соединений наружной коробки, переплетов размечают аналогично по приведенной формуле.
Сборка оконных блоков. Сборка оконных блоков состоит из следующих операций: сначала проводят сборки оконных створок, форточек, фрамуг на клею; выдерживают склеенные створки, форточки, фрамуги; обрабатывают их по периметру; зачищают провесы; проводят выборку паза под отлив; прорезают или выбирают гнезда под петли; проводят пригонку форточек; навешивают на петли; устанавливают отлив, нащельник; собирают блок коробки; производят вгонку и навешивают створки. Фрамугу ставят в коробку.
Створки, фрамуги, форточки собирают на рабочем столе или в сборочных станках. Сначала бруски подбирают, тщательно подгоняя углы, и проверяют плотность сопряжений. Шипы и проушины намазывают клеем, после чего соединяют бруски в рамку (створку).
В углах соединений коловоротом со спиральным сверлом просверливают отверстия, в которые вставляют деревянный нагель (круглый стержень сечением по диаметру отверстия), предварительно намазанный клеем.
Оконные коробки с вгонкой в них переплетов удобнее собирать вдвоем. Шипы брусков смазывают клеем, собирают и обжимают в сборочном станке неотложной конструкции.
Сборочный станок представляет собой металлические козлы (рис. 4 ) высотой 600 и длиной 1600 мм. Сверху сборочного станка расположен металлический швеллер №10, на котором имеются переставной упор и винтовое устройство. Наличие в швеллере ряда отверстий на расстоянии друг от друга 100 мм позволяет устанавливать упор на нужном расстояния от винтового устройства.
После сборки проверяют прямоугольность коробки путем замера по диагонали, сверлят в ее углах отверстия и вставляют в отверстия нагели.
Собранные оконные створки, фрамуги и коробки должны иметь по периметру припуск на дальнейшую обработку до 3-4 мм и по толщине 1 мм для снятия провесов.
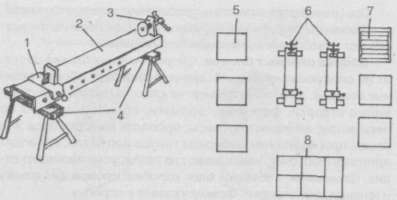 |
Рис. 4. Сборочный станок конструкции Я. Ерохина и рабочее место для сборки оконных блоков: 1 - переставной упор; 2 - швеллер; 3 - винтовое устройство; 4 - козлы; 5 - детали створок; 6 - станки Ерохина; 7 - детали коробок; 8 - собранные коробки |
По периметру створки и фрамуги обрабатывают после схватывания клея в шиповых соединениях. Если изделие обрабатывать сразу после сборки без выдержки, то клеевое соединение нарушится.
Обработку по периметру производят фуганком или электрорубанком, для чего предварительно закрепляют створку в вертикальном положении в верстаке. Створки, фрамуги, форточки можно обрабатывать также на фрезерном станке в шаблонах. Провесы в плоскости створок, фрамуг и форточек снимают ручным инструментом (рубанком, фуганком), небольшие провесы - на шлифовальных станках.
После обработки по периметру переплеты навешивают на петли в коробки, а затем ставят раскладки, отливы и приборы.
Для выполнения этих операций используют верстак, оборудованный приспособлением для дисковой вилы. Приспособление служит для перепиливания раскладок и других деталей под любым углом и представляет собой дисковую электропилу с рамой, изготовленной из уголков сечением 30x30x4 мм. Рама длиной 700 мм одним концом прикрепле-
на к шарнирному стопору, который вместе с упорным бруском неподвижно закреплен на верстаке. Благодаря шарниру-стопору рама может поворачиваться под нужным углом к упорному бруску и стопориться.
Чтобы перепилить деталь, раму необходимо установить под нужным углом к упорному бруску, затем вплотную подвинуть к нему деталь и включить дисковую электропилу.
Трудоемкая операция - врезка петель. Для разметки гнезд применяют шаблон Павлихина, представляющий собой деревянную рейку с упором и двумя скобами с заточенными фасками. Размеры скоб соответствуют размерам петель.
При разметке шаблон кладут на кромку створки по упору, а затем легким ударом киянкой по скобе переносят ее отпечаток на створку и по нему в дальнейшем выбирают гнездо под петлю. Аналогично делают разметку на коробках. По разметке стамеской выбирают гнезда под петли. Упор у стамески позволяет заглублять лезвие на заданный размер. Глубина гнезда под петлю должна соответствовать ее толщине, с тем чтобы после установки поверхность петли была заподлицо с древесиной.
Вгоняют и навешивают створки в коробку на специальных столах. Процесс вгонки и навешивания оконных створок в коробку состоит из следующих основных операций: подготовка створок, зачистка провесов, навешивание на петли, устранение возможных дефектов (заколов, неровностей), упаковка блока для передачи его под окраску.
При вгонке переплетов в коробку сначала навешивают наружные переплеты. При изготовлении переплетов с фрамугой подгоняют прежде всего фрамугу, а затем створки. Зазор между створками и коробкой должен быть не более 2 мм, что необходимо для последующего покрытия створок слоем краски.
При подгонке створок, тщательно проверяют правильность притвора, плотность их прилегания к четвертям коробки. Необходимо следить за тем, чтобы навешенные створки открывались свободно, плавно и не пружинили. Внутренние створки подгоняют к коробке так же, как и наружные. При подгонке следят за там, чтобы все элементы оконного блока были гладко обработаны и в месте соединения (фальцовки) тщательно пригнаны.
Клей с поверхности элементов блока должен быть счищен.
Петли в брусках створки, форточки, фрамуги должны быть врезаны заподлицо, иначе створки не будут плотно закрываться и будут пружинить. Число шурупов для крепления петель к створкам, фрамугам, форточкам, коробкам должно соответствовать числу отверстий. Петли в окнах врезают на расстоянии 200 мм от четверти коробки.
Створки высотой 795 мм и шириной 420 мм включительно навешивают на накладные петли ПНЦ70 с ходом на центрах или на фигурные петли ПНФЦ70, а створки высотой 795,1095, 1395 и 1690 мм и шириной 420-845 мм - на петли накладные ПНЦ85 или ПНФЦ85.
Створки высотой 795, 1095, 1395 мм, но шириной более 845 мм навешивают на накладные петли ПНШ85 и ПНФШ85 с ходом на шарике или на петли ПНЦ110 и ПНФЦ110 сходом на центрах.
Форточки шириной до 447 мм навешивают на накладные петли ПНС40 со сквозным стержнем, а шириной более 447 мм - на петли ПНС60.
Спаренные створки, фрамуги шириной до 695 мм соединяют накладными петлями ПНО80 с ограничителем подъема, створки шириной 720 мм и более - петлями ПН0110.
Ручки, остановы, запорные приборы устанавливают на оконных блоках в процессе монтажа. Для закрывания переплетов в спаренных створках врезают завертки вручную или с помощью электродолбежника и электросверла.
Навешенные на петли створки соединяют винтовыми стяжками. Гнезда под стяжки выбирают сверлом, долотом, стамеской, производимой по шаблону или по их контуру.
Технические условия для окон. Допускается увеличение номинальных размеров зазоров в притворах не более 1 мм для элементов размером до 1500 мм и 1,5 мм для элементов свыше 1500 мм. Покорюбленность и перекосы изделий и деталей не должны быть более 0,7мм на 1 м.
Окна изготовляют из древесины хвойных пород: сосны, ели, пихты, кедра, лиственницы. Внутренние фрамуги, устраиваемые в помещениях с относительной влажностью воздуха
до 60%, можно изготовлять из древесины березы, осины, бука, ольхи, липы и тополя.
Шиповые соединения деталей окон выполняют концевыми на открытые сквозные шипы, а вертикальные импосты - на сквозные шипы или шканты. Горизонтальные соединения серединные делают на несквозные шипы. Шиповые соединения дополнительно крепят угольниками с шурупами по двум верхним углам шиповых соединений на внутренних створках высотой более 1500, шириной 600-800 мм, на внутренних фрамугах и полотнах в блоках с раздельными элементами, а также на наружных полотнах балконных блоков со спаренными и раздельными элементами. На внутренних створках шириной свыше 800 мм в блоках с раздельными переплетами и на наружных створках и фрамугах всех размеров блоков с раздельными и спаренными переплетами угольники ставят по четырем углам.
Отливы и нащельники устанавливают на клеях повышенной водостойкости, дополнительно прикрепляя их шурупами с шагом 250 мм. Длина шурупа должна быть не менее двойной толщины нащельника или отлива. Отлив должен крепиться шурупами не менее чем в трех точках.
Окна могут иметь непрозрачную и прозрачную отделку. Непрозрачная отделка производится масляными красками, эмалями, а прозрачная- прозрачными лаками. Качество вскрытия зависит от качества поверхности. Поверхности коробок окон, примыкающие к каменной кладке, бетону, штукатурке, а также эксплуатируемые в помещениях с относительной влажностью свыше 60%, должны быть антисептированы или окрашены.